News & Press
How surface roughness influences the adhesion of soft materials
Research team discovers universal mechanism that leads to adhesion hysteresis in soft materials
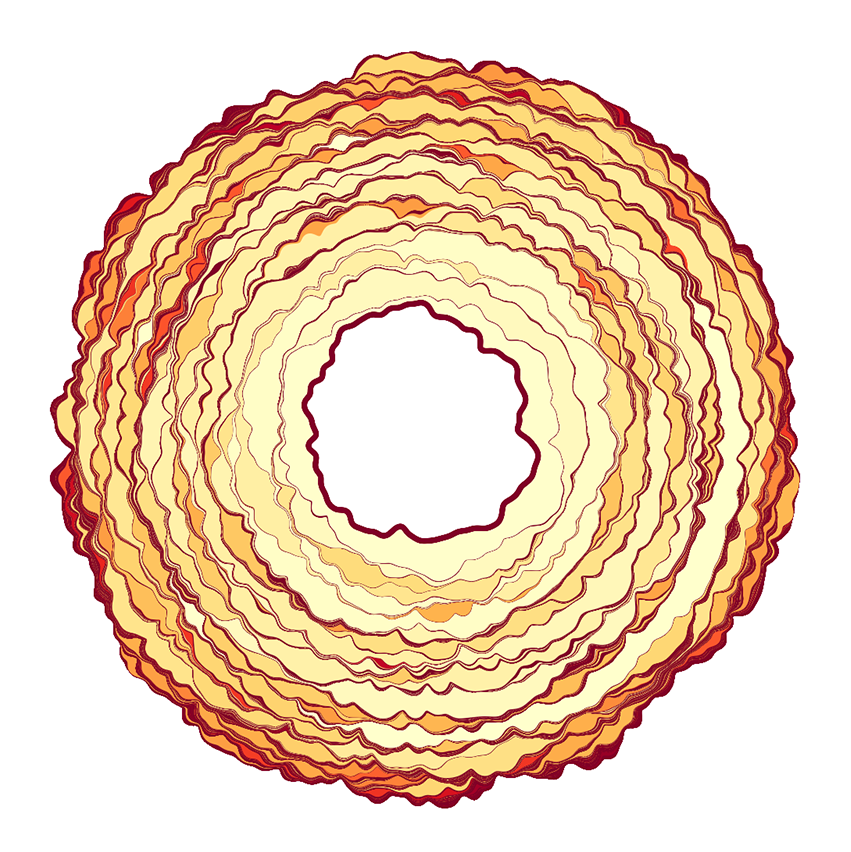
The simulation shows the contact area of a soft solid that is separated from a rough surface. Each coloured spot corresponds to an instability of the contact. The different colour intensity shows how much energy is lost in the process. Source: Antoine Sanner, Lars Pastewka.
Adhesive tape or sticky notes are easy to attach to a surface, but are difficult to remove. This phenomenon, known as adhesion hysteresis, can be fundamentally observed in soft, elastic materials: Adhesive contact is formed more easily than it is broken. Researchers at the University of Freiburg, the University of Pittsburgh and the University of Akron in the US have now discovered that this adhesion hysteresis is caused by the surface roughness of the adherent soft materials. Through a combination of experimental observations and simulations, the team demonstrated that roughness interferes with the separation process, causing the materials to detach in minute, abrupt movements, which release parts of the adhesive bond incrementally. Dr. Antoine Sanner and Prof. Dr. Lars Pastewka from the Department of Microsystems Engineering and the livMatS Cluster of Excellence at the University of Freiburg, Dr. Nityanshu Kumar and Prof. Dr. Ali Dhinojwala from the University of Akron and Prof. Dr. Tevis Jacobs from the University of Pittsburgh have published their results in the prestigious journal Science Advances.
“Our findings will make it possible to specifically control the adhesion properties of soft materials through surface roughness,” says Sanner. “They will also allow new and improved applications to be developed in soft robotics or production technology in the future, for example for grippers or placement systems.”
Sudden jumping movement of the edge of the contact
Until now, researchers have hypothesized that viscoelastic energy dissipation causes adhesion hysteresis in soft solids. In other words, energy is lost to heat in the material because it deforms in the contact cycle: It is compressed when making contact and expands during release. Those energy losses counteract the movement of the contact surface, which increases the adhesive force during separation. Contact ageing, i.e. the formation of chemical bonds on the contact surface, has also been suggested as a cause. Here the longer the contact exists, the greater the adhesion. “Our simulations show that the observed hysteresis can be explained without these specific energy dissipation mechanisms. The only source of energy dissipation in our numerical model is the sudden jumping movement of the edge of the contact, which is induced by the roughness,” says Sanner.
Adhesion hysteresis calculated for realistic surface roughness
This sudden jumping motion is clearly recognisable in the simulations of the Freiburg researchers and in the adhesion experiments of the University of Akron. “The abrupt change in the contact surface was already mentioned in the 1990s as a possible cause of adhesion hysteresis, but previous theoretical work on this was limited to simplified surface properties," explains Kumar. “We have succeeded for the first time in calculating the adhesion hysteresis for realistic surface roughness. This is based on the efficiency of the numerical model and an extremely detailed surface characterisation carried out by researchers at the University of Pittsburgh,” says Jacobs.
About the Cluster of Excellence livMatS
The vision of the Cluster of Excellence Living, Adaptive, and Energy-Autonomous Materials Systems (livMatS) is to combine the best of both worlds – nature and technology. livMatS develops lifelike materials systems inspired by nature. These systems adapt autonomously to their environment, harvest clean energy from their surroundings, and are insensitive to or able to recover from damage.
- Original publication: Antoine Sanner et al., Sci. Adv. 10, eadl1277 (2024). doi: 10.1126/sciadv.adl1277.
- Prof. Dr. Lars Pastewka has been Professor of Simulation at the Faculty of Engineering and a member of the Cluster of Excellence Living, Adaptive and Energy-autonomous Materials Systems (livMatS) at the University of Freiburg since 2017.
- Dr. Antoine Sanner completed his doctorate at the Department of Microsystems Engineering and in the Cluster of Excellence livMatS.
- The study was funded by the German Research Foundation (livMatS - EXC 2193), the European Research Council (StG 757343), the National Science Foundation (DMR-2208464) and the National Institute for Occupational Safety and Health (R21 OH012126).
Contact:
Office of University and Science Communications
University of Freiburg
Tel.: 0761/203-4302
e-mail: kommunikation@zv.uni-freiburg.de