News & Presse
Intelligente Flugzeugflügel könnten Sprit sparen
Chris Eberl entwirft Elementarzellen – diese Miniaturbausteine verleihen Materialien besondere Fähigkeiten
Bausteine in Feinstaubdimension: Gerade einmal einen hundertstel Millimeter sind die Elementarzellen groß, die der Mikromechaniker Prof. Dr. Chris Eberl im Freiburger Exzellenzcluster livMatS – Living, Adaptive and Energy-autonomous Materials Systems entwickelt. Die Geometrie der Zellen entscheidet mit darüber, was die aus ihnen bestehenden Metamaterialien können. Aus solchen intelligenten Materialien gefertigte Flugzeugflügel könnten sich bei entsprechender Reisegeschwindigkeit so günstig verformen, dass sie Sprit oder Biosprit sparen.
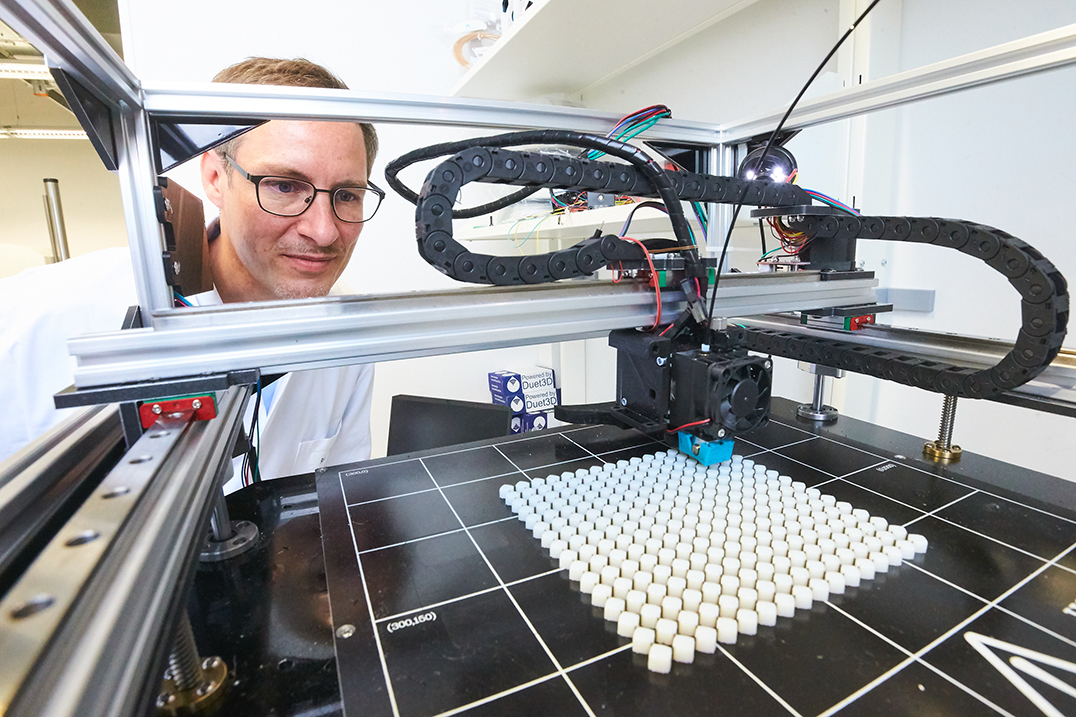
Bauteile aus dem 3-D-Drucker: Das „shape morphing“, die Formveränderung von Materialien, gehört zu Chris Eberls Schwerpunkten. Foto: Harald Neumann
Flugzeuge könnten klimaschonender fliegen. „Wenn sich ihre Flügel bei Reisegeschwindigkeit günstig verformen würden, könnten sie ihre Aerodynamik verbessern und Sprit oder Biosprit sparen“, sagt Chris Eberl. Der Professor für Mikro- und Werkstoffmechanik vom Institut für Mikrosystemtechnik (IMTEK) forscht an intelligenten Materialien. Ein Thema seiner Arbeit ist „shape morphing“, Formveränderung. Damit will Eberl, der auch stellvertretender Leiter am Fraunhofer-Institut für Werkstoffmechanik IWM ist, Flugzeuge irgendwann in die Lage versetzen, dass sich ihre Flügel selbstständig verformen. Die sollen am Luftwiderstand und anderen Messwerten erkennen, wann welche Veränderungen angebracht sind. „Solche Fähigkeiten programmieren wir in die Struktur von Materialien ein“, erklärt der Wissenschaftler: „Sie sollen sich so verhalten, als ob sie leben würden.“
Jede Elementarzelle erfüllt eigene Bedürfnisse
Die Forscherinnen und Forscher von livMatS entwickeln Materialsysteme, die sich äußeren Gegebenheiten anpassen, richtig darauf reagieren, dazu lernen und sich nötigenfalls selbst reparieren. Eberl spricht von „Wenn-dann-Beziehungen“: Wenn der Luftwiderstand den Wert erreicht, den er bei Reisegeschwindigkeit hat, dann morphen die Flügel. „Wenn-dann-Beziehungen können wir in die Geometrie von Elementarzellen einprogrammieren“, sagt der Mikromechaniker. In seinen Materialien sind die Elementarzellen die kleinesten Baueinheiten, so wie die Schaumblasen im Schaumstoff. Flink zeichnet er ein paar Designs auf – unterschiedliche geformte Kästchen mit elastischen, verschieden gefalteten Wänden, die unterschiedliche Verstärkungen haben.
Ein anderer Aufbau bedeutet andere Eigenschaften. Eberl kann Elementarzellen viele Fähigkeiten über ihre Geometrie verleihen. Sie kann etwa bewirken, dass sich Materialien bei Druck lokal versteifen, weil sich die Elementarzellen nur begrenzt verformen – bis dahin, wo Verstärkungen ihrer Wände aneinanderstoßen. „Grundsätzlich könnten wir die Energie des Drucks nutzen.“ Statt nur aneinanderzustoßen, könnten Wandverstärkungen unter Druck einrasten wie Druckknöpfe an Sprungfedern. Ein Klick, und die Druckenergie wäre gespeichert. Sie würde dann wieder frei, wenn sich die „Druckknöpfe“ unter festgelegten Bedingungen lösen.
„Die Designs der Elementarzellen beruhen auf Erfahrung, Kreativität, Intuition und viel Optimierung“, erklärt Eberl und fügt an: „Aktuell können wir einzelne Zellen erzeugen und lernen gerade, wie wir sie ein System integrieren.“ Es gibt einige Hürden: Elementarzellen haben Feinstaubdimension. „Sie sind ungefähr zehn Mikrometer winzig – einen Hundertstelmillimeter.“ Außerdem treten die Zellen miteinander in Wechselwirkung. Um erneut den Schaumstoffvergleich zu bemühen: Wenn Druck auf ihn kommt, geben die Blasen Teile davon an ihre Nachbarblasen weiter. Jede Blase verformt sich ein bisschen anders. „Genauso erfüllt in intelligenten Materialien jede Elementarzelle verschiedene Bedürfnisse“, betont Eberl, „und die müssen wir jeweils mit hohem Aufwand einstellen.“
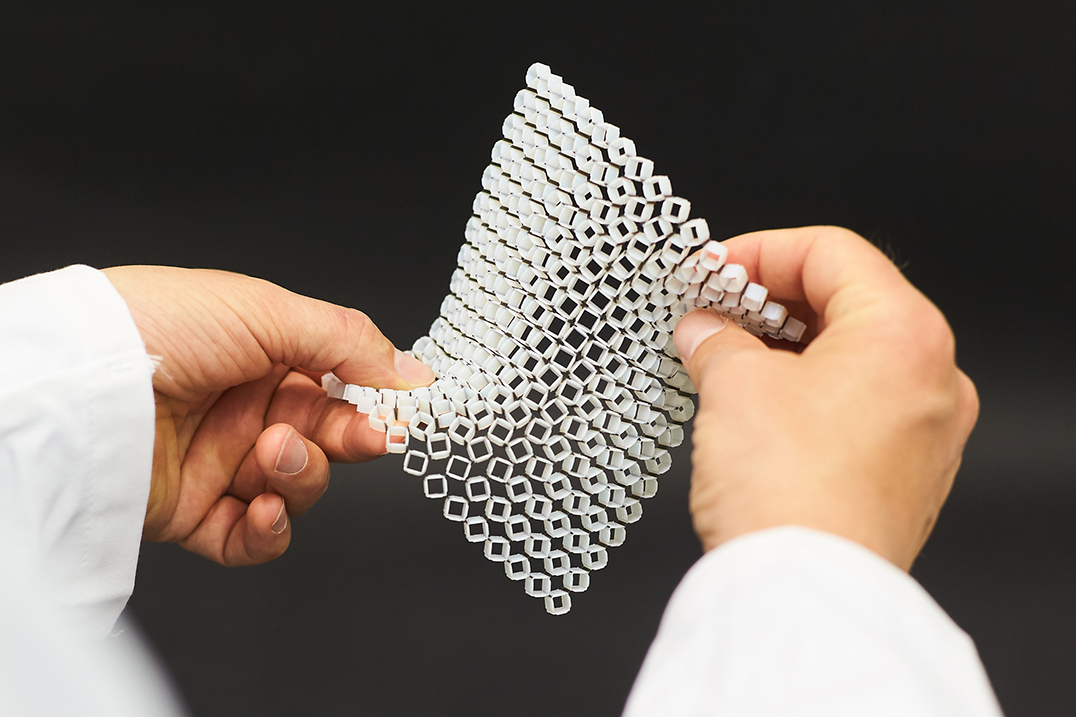
Ein Modell zeigt ein Netz von Elementarzellen: Ihre Substanz sollte ungiftig, recyclingfähig und preiswert sein. Foto: Harald Neumann
Ungiftig, recyclingfähig, preiswert
Das geht nur, wenn der Baustoff ebenfalls passt: „Von ihm hängt ab, wie fein Elementarzellen sein können und wie dick und steif oder flexibel ihre Wände geraten.“ Außerdem sollte die Substanz ungiftig, recyclingfähig und preiswert sein. livMatS setzt auf nachhaltige, wirtschaftliche und industrietaugliche Materialsysteme. Darum achtet Eberl darauf, dass die Herstellung nicht zu kostspielig wird, auch was die Methoden betrifft. Die winzigsten Strukturen erzeugt sein 10-köpfiges Team mit Zwei-Photonen-Lithographie, einem extrem präzisen 3-D-Druckverfahren. Das ist teuer. Größere Bauteile entstehen darum im üblichen 3-D-Druck und noch größere, mechanische mittels Spritzguss oder Folienverfahren.
Damit nicht genug: Die Materialsysteme aus Eberls Kooperationsprojekten müssen fehlerfrei arbeiten. Intelligente Flugzeugflügel dürfen sich durch kurze, abrupte Windstöße nicht falsch verformen. Das Material muss Störungen und Normalzustand unterscheiden können. Stabilität ist ebenso gefragt. Die Flügel dürfen sich nur an vorgesehenen Stellen verformen, aber dort auch nicht brechen. Damit ist der Kriterienkatalog längst nicht abgehakt: Die Materialsysteme sind bioinspiriert. „Wir übernehmen Konzepte aus der Natur, nicht um sie nachzubauen, sondern um sie grundlegend zu verstehen und für andere Zwecke zu adaptieren.“
Ganz schön viele Anforderungen. „Wir nehmen sie als Herausforderung für die Forschung“, zeigt sich Eberl gelassen. Gerade die Größe und Vielfalt der Fachdisziplinen in den livMatS-Kooperationen ermögliche es, mehrere Ziele zu verfolgen: „Da läuft viel parallel.“ Kooperationspartnerinnen und -partner entwickeln etwa neue Bausubstanzen, testen Zelltypen oder simulieren Materialsysteme am Computer detailliert über alle Größenskalen hinweg: „Damit verstehen wir sie vom Molekül bis zum Bauteil.“ Er nennt noch einen Vorteil der Zusammenarbeit: „Wir können nicht nur rein technologisch an Projekte herangehen.“
Was bedeutet Lernen bei Materialien?
livMatS befasst sich beispielsweise mit Fragen, was Lernen bei Materialien tatsächlich bedeutet. „Ein Stab aus relativ steifem Material könnte lernen, sich an nur einer Stelle zu biegen“, nennt der Mikromechaniker ein Beispiel: Mehrfaches Biegen an besagter Stelle könnte dazu führen, dass sich dort Moleküle umlagern. Der Stab würde lokal erweichen und bekäme eine Soll-Biegestelle. Kann man das schon als Lernen bezeichnen? „Ich glaube nicht“, sagt Eberl. Dem Stab fehle eben das Feedback – die Wurst oder der Tadel, den Hunde erhalten, nachdem sie Aufgaben richtig oder falsch gemacht haben.
Bei all diesen Ansprüchen werden selbstbiegende Flugzeugflügel noch ein bisschen auf sich warten lassen. Doch Eberl hofft, in zwei Jahren ein Materialsystem zu haben, das einfache Grundfunktionen erfüllt, möglichst ausdauernd ist, fähig zum Recycling und zuverlässig arbeitet. Dafür werden sich auch seine Kooperationspartner ins Zeug legen: Dr. Olga Speck, die Biomimetikspezialistin vom Botanischen Garten der Universität steuert Anregungen und Konzepte aus der Pflanzenwelt bei. Prof. Dr. Jürgen Rühe vom IMTEK entwickelt und optimiert Strukturmaterialien. Prof. Dr. Lars Pastewka, ebenfalls vom IMTEK, modelliert die Materialsysteme am Computer vom Molekül bis zum Bauteil.
Jürgen Schickinger
Weitere Artikel dieser Serie:
Die künstliche Falle
Kleines, scharfes Auge
Eine Sprache für die Spuren zwischen Natur und Technik
Flächen-Intimität, die Strom erzeugt